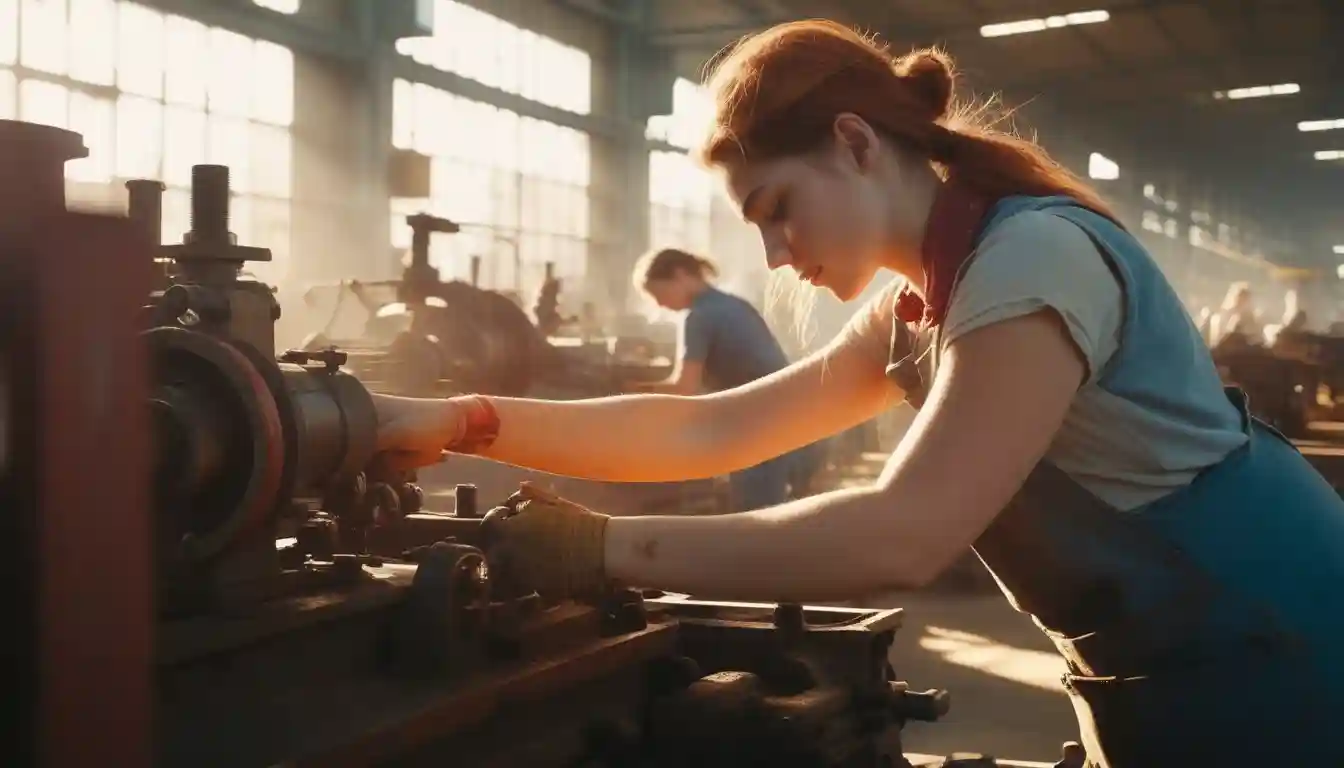
Manufacturing's Generational Reckoning - The Gen Z Workforce Dilemma Reshaping American Industry
Manufacturing's Generational Reckoning: The Gen Z Workforce Dilemma Reshaping American Industry
A Digital Generation Meets an Industry in Flux
DETROIT — On the immaculate floor of a recently upgraded Midwestern manufacturing facility, robotic arms pivot with balletic precision while a solitary technician monitors multiple workstations through an augmented reality interface. The scene represents both the promise and the paradox facing American manufacturing in 2025: unprecedented technological sophistication alongside persistent workforce challenges that threaten to undermine the sector's revival.
"We've invested over $30 million in automation upgrades across our facilities in the past eighteen months," explains the operations director at this plant. "The technology is transforming what we can accomplish with fewer people on the floor. But finding qualified staff who can manage these systems? That's become our biggest constraint to growth."
This facility's experience mirrors a nationwide phenomenon. Despite the manufacturing sector adding 29,000 jobs in transportation and warehousing this April, companies are struggling with a staggering 449,000 unfilled positions as of March—a number that has actually increased from February's 445,000 vacancies. The productivity statistics tell an equally revealing story: manufacturing labor productivity surged 4.5% in the first quarter of 2025, with output increasing 5.1% while hours worked grew by just 0.5%.
Behind these figures lies a profound generational disconnect between the manufacturing industry and Generation Z workers now entering the workforce in significant numbers. This disconnect may determine whether American manufacturing can sustain its technological transformation or whether it will face structural constraints that limit its resurgence.
The Crisis of Perception vs. Reality
In a gleaming conference room at a workforce development agency in Cincinnati, career counselor Melissa scrolls through survey results on her tablet with visible concern. "These numbers are troubling, but they explain so much of what we're seeing on the ground," she says.
The survey she references reveals that only 14% of Gen Z would consider industrial work as a long-term career, while 26% would entertain such positions only as short-term employment. Most striking is that 38% of Gen Z respondents acknowledge they're unaware of industrial workers' roles and responsibilities—a knowledge vacuum allowing outdated perceptions to persist unchallenged.
"Young people come in with images of their grandparents' factory jobs—repetitive, physically demanding, dirty work without much future," Hernandez explains. "They simply don't see the connection between their digital skills and modern manufacturing environments."
This perception gap extends to compensation, with approximately 20% of Gen Z believing industrial work offers substandard pay. The reality contradicts this perception dramatically. Manufacturing Engineers now earn an average annual salary of $85,613, with top performers commanding $109,500 annually. Manufacturing Production Managers receive an average of $74,500 annually, with the upper quartile earning $86,500. These figures represent substantial compensation for roles often accessible without advanced degrees.
The manufacturing sector has responded to labor market tightness by accelerating wage growth, with average hourly earnings reaching $35.06 in early 2025—a 4.3% year-over-year increase that outpaces inflation. Regional disparities create additional opportunities, with Manufacturing Engineers in California earning substantially more than the national average at $94,498 annually, and certain specialized markets like Soledad, CA offering Manufacturing Engineers annual salaries of $128,069.
"When I show these salary figures to young people in our career workshops, their jaws drop," Melissa notes. "Most had no idea these positions paid so well."
A Sector Fighting for Its Future Workforce
The implications of manufacturing's workforce challenges extend far beyond individual companies. Once the backbone of middle-class opportunity in America, manufacturing jobs represented approximately 22% of the workforce in 1979 but had contracted dramatically to just 8% by 2024.
The Trump administration has highlighted manufacturing growth as a policy priority, with White House Press Secretary Karoline Leavitt recently noting that "the manufacturing industry is already rebounding, as there were 9,000 new auto jobs created—the most auto jobs added in 15 months." Commerce Secretary Howard Lutnick articulated an even more ambitious vision, claiming "the tradecraft of America, our high school-educated Americans, the core to our workforce, is going to have the greatest resurgence of jobs in the history of America, to work on these high-tech factories, which are all coming to America."
Industry analysts view such pronouncements with cautious skepticism. "The administration's optimism focuses on absolute job numbers without addressing the fundamental demographic and perception challenges facing the sector," observes a manufacturing policy specialist at a leading economic think tank. "Adding 9,000 auto jobs is positive, but it doesn't solve the deeper structural problem of young workers avoiding manufacturing careers."
The workforce stability picture adds another layer of complexity. After reaching historically high levels in 2022, overall manufacturing turnover decreased to 16.12% in 2023, approaching pre-pandemic levels. However, other analyses present a more alarming picture, with some sources indicating current manufacturing employee turnover has reached 39.9%, representing a 306% increase from 2017 levels.
"Turnover at these rates is financially devastating," explains an industrial psychologist who consults with manufacturing firms on retention strategies. "When an experienced machinist or technician leaves, companies aren't just losing an employee—they're losing institutional knowledge that often can't be replaced quickly even with substantial wage offers."
Digital Natives Meet Digital Factories
The technological transformation sweeping through manufacturing creates natural alignment with Gen Z's digital fluency—if only the connection can be effectively communicated. As the first truly digital-native generation, Gen Z brings sophisticated technological literacy that could prove invaluable to manufacturing organizations navigating digital transformation.
"When we show young people our facility, their entire perspective changes," says the training director at a precision manufacturing company in North Carolina. "They're shocked to see how much of our operation involves programming, digital interfaces, and problem-solving rather than repetitive physical labor."
Modern manufacturing increasingly leverages technologies that could appeal to Gen Z's expectations: artificial intelligence applications for safety monitoring, advanced detection systems that identify potential hazards 10-12 times faster than traditional methods, and digital workflow tools that mirror the technological sophistication Gen Z experiences in their personal digital lives.
The receptiveness of Gen Z to manufacturing automation appears more positive than commonly assumed, with 48% of Gen Z respondents in one study reporting they were either "excited" or "optimistic" about automation's impact on manufacturing. This technological optimism represents a potential bridge between manufacturing employers and Gen Z talent.
"Our most successful recent hires have been gamers," notes an operations manager at an advanced electronics manufacturer. "The spatial reasoning, pattern recognition, and quick decision-making they've developed translate perfectly to our production environment. We just need to help them see that connection."
Research indicates that demand for digital roles in manufacturing—including statisticians, data scientists, computer experts, and information systems managers—has surged by 75% over the past five years, creating opportunities that align with Gen Z career aspirations.
The Regional Renaissance Phenomenon
While national manufacturing trends provide important context, regional manufacturing ecosystems demonstrate remarkable variability. Alabama offers an instructive case study in manufacturing revitalization, with Representative Dale Strong highlighting the state's trajectory: "You look at the jobs that we've brought in the last 10 or 15 years. You start with GE Aviation, Polaris, Toyota Motor Manufacturing, Mazda Toyota. We've proven that the Alabama workforce has the ability. I think our finest hours are still ahead."
Similar manufacturing clusters have developed in parts of Tennessee, Michigan, and Texas, often built around specific industry verticals and supported by targeted workforce development initiatives.
"The most successful regional manufacturing economies have created ecosystems connecting educational institutions, industry partners, and economic development agencies," explains an economic development specialist focusing on manufacturing revival. "These partnerships are addressing both immediate workforce needs and longer-term pipeline development."
These regional success stories demonstrate how targeted economic development strategies, workforce development initiatives, and public-private partnerships can generate manufacturing growth even amid national challenges.
Reimagining Recruitment for a New Generation
Progressive manufacturing organizations are fundamentally rethinking their approach to talent acquisition and retention based on Gen Z priorities.
Work model flexibility represents a particular challenge, with 84% of Gen Z favoring arrangements that provide choices in when and where work occurs. While manufacturing has traditionally required on-site presence, innovative organizations are identifying roles suitable for partial remote work and implementing flexible scheduling within production constraints.
"We've moved to a four-day, 10-hour shift model for certain production teams, and it's been transformative for retention," explains a human resources director at a mid-sized manufacturer in Pennsylvania. "Our younger employees get a three-day weekend every week, which they value enormously, and we've seen productivity increase despite fewer days on-site."
Purpose-driven employment represents another critical factor for Gen Z. "Young people don't just want a paycheck—they want to understand how their work contributes to something meaningful," says a manufacturing recruiter specializing in early-career placement. "Companies making medical devices or renewable energy components have a built-in advantage, but every manufacturer needs to articulate purpose beyond profit."
Career pathway transparency emerges as a decisive factor, with 32% of Gen Z willing to consider industrial work if clear corporate advancement paths exist. "When we implemented a structured technical career ladder with transparent promotion criteria and mentorship programs, our application rates from recent graduates doubled," reports the talent acquisition manager at a precision aerospace components manufacturer.
The Economic Implications of Manufacturing's Workforce Challenge
The manufacturing sector's struggles to attract Gen Z talent have profound implications for the broader economy. Manufacturing sector labor productivity has grown at an annualized rate of 0.5% during the current business cycle, outperforming the previous cycle's 0.1% growth rate, though still below the long-term rate of 2.1% since 1987.
"We're seeing the beginning of a capital-deepening super-cycle driven by labor scarcity," explains a senior analyst at a major investment firm tracking manufacturing trends. "Companies can't find workers, so they're investing heavily in automation, AI, and advanced manufacturing technologies. This drives productivity gains but fundamentally changes the relationship between manufacturing output and employment."
This transition creates both winners and losers in the manufacturing landscape. Companies at the technological frontier that successfully attract digitally fluent workers are pulling ahead in productivity and profitability. Meanwhile, firms reliant on traditional labor-intensive processes face mounting challenges from both workforce shortages and wage pressures.
"The manufacturing sector is bifurcating," observes an economist specializing in industrial organization. "Digital leaders are evolving toward something resembling software companies—high fixed costs, low variable labor costs, and winner-takes-all productivity advantages. Labor-intensive producers are caught in a margin squeeze between rising wages and inability to pass costs through to customers."
This divergence has implications for communities historically dependent on manufacturing employment. While aggregate manufacturing output continues to grow, the distribution of economic benefits is shifting toward regions and demographic groups positioned to participate in digitally transformed manufacturing.
The Path Forward: Bridging the Generational Divide
Manufacturing institute President Carolyn frames the challenge in stark terms: "Pandemic-driven shifts have already created hundreds of thousands of new jobs, and now we are seeing increased demand for digital skills that need to be met or risk further widening of the talent gap."
The path forward requires concerted action across multiple dimensions:
Educational institutions must evolve curricula to reflect modern manufacturing realities, incorporating digital skills, automation familiarity, and problem-solving competencies relevant to advanced manufacturing environments.
Manufacturing employers must fundamentally rethink recruitment approaches, workplace policies, and career development structures to align with Gen Z expectations while effectively communicating the sector's evolving nature.
Policymakers must recognize that manufacturing revival requires more than favorable trade policies or investment incentives—it demands coordinated investment in workforce development pipelines aligned with emerging industry needs.
The manufacturing sector in 2025 stands at a pivotal moment, facing both unprecedented challenges and transformative opportunities. The companies and regions that successfully bridge the generational divide will shape not only their own futures but the trajectory of American industrial competitiveness for decades to come.
"Manufacturing is not just about innovation and economic growth; it's about opportunity," Carolyn observed. "It's about ensuring that every community, every aspiring maker, builder and creator—no matter their background—can have access to the skills, training and careers that will define the future."
SIDEBAR: The Investment Landscape: Following the Manufacturing Transformation
As manufacturing navigates its workforce transformation, capital is flowing toward companies positioned to benefit from the sector's evolution. Investment analysts identify several categories of likely winners:
-
Automation and vision systems providers are seeing order books grow in direct proportion to workforce vacancies, with projections of 12-15% annual revenue growth while manufacturing job openings remain above 300,000.
-
Field service marketplaces and predictive maintenance software benefit from the expanding installed base of manufacturing technology, with every new robot or advanced system creating ongoing service requirements.
-
Workforce development platforms specializing in industrial skills are experiencing surging demand, with demographic scarcity giving them unusual pricing power and customer retention.
Conversely, labor-intensive tier-2 suppliers in sectors like textiles and fabricated metals face margin pressures as labor costs rise faster than their ability to automate or pass costs through to customers. Legacy manufacturers slow to digitize operations bear the full weight of elevated turnover rates and struggle to attract next-generation talent.
"We're advising clients to think of manufacturing more like software—focusing on companies with high fixed costs, low variable labor costs, and winner-takes-all productivity advantages," explains a portfolio manager specializing in industrial transformation. "The old metrics of success like headcount growth are giving way to new measures like revenue per employee and digital skills density."
This perspective shift has profound implications for capital allocation, with increasing premiums for manufacturing companies demonstrating technological leadership and workforce development innovation while discounting traditional manufacturing business models regardless of short-term financial performance.
DATA SPOTLIGHT: Key Manufacturing Workforce Metrics
Unfilled Manufacturing Jobs: 449,000 positions as of March 2025, up from 445,000 in February 2025.
Manufacturing Productivity Growth: 4.5% increase in Q1 2025, driven by 5.1% output growth while hours worked increased only 0.5%.
Average Manufacturing Hourly Wage: $35.06 as of April 2025, representing 4.3% year-over-year growth exceeding inflation.
Manufacturing Turnover Rate: 16.12% in 2023 (approaching pre-pandemic levels), but some analyses indicate current rates may be as high as 39.9%.
Gen Z Career Interest: Only 14% of Gen Z would consider industrial work as a long-term career path.
Manufacturing Knowledge Gap: 38% of Gen Z acknowledge they are unaware of industrial workers' roles and responsibilities.
Technological Receptiveness: 48% of Gen Z report being either "excited" or "optimistic" about automation's impact on manufacturing.
Regional Wage Disparities: Manufacturing Engineers in California earn average annual compensation of $94,498 compared to the national average of $85,613, with certain specialized markets like Soledad, CA offering annual salaries of $128,069.