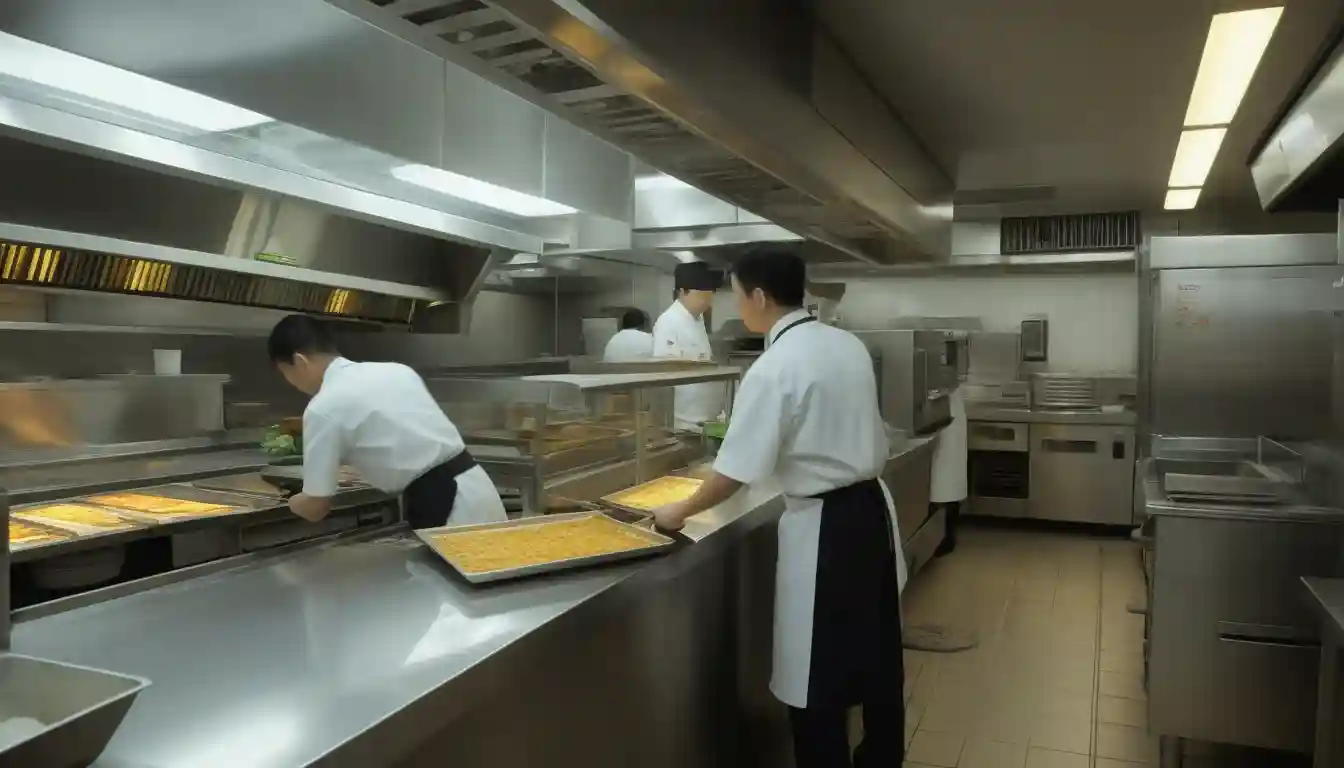
McDonald's China Revolutionizes Food Safety and Supply Chain with Groundbreaking 'One Box, One Code' Technology
McDonald's China Leads Supply Chain Innovation with Breakthrough Digital Tracking Technology
McDonald's China has unveiled a pioneering advancement in supply chain management with the introduction of its "One Box, One Code" technology. Presented at the China International Supply Chain Expo on November 27, 2024, this new digital solution marks the first large-scale implementation of this kind in the Chinese food service industry. By leveraging RFID (Radio Frequency Identification) and IoT (Internet of Things) technologies, McDonald's is revolutionizing its supply chain with enhanced transparency, efficiency, and safety—factors that are crucial in today's highly dynamic food sector.
Introducing the "One Box, One Code" Technology
McDonald's China has taken a significant leap in digitalizing its supply chain through the use of RFID and IoT technologies to assign unique identifiers, or "digital IDs," to every box of goods. These "digital passports" ensure that each item can be traced throughout the entire supply chain, from manufacturing facilities to restaurants. By deploying this technology, McDonald's aims to achieve real-time tracking, enabling a higher level of transparency and efficiency in managing goods.
The development of this system began in 2022, when McDonald's China, in collaboration with Cainiao—a leading IoT solutions provider—started exploring ways to utilize RFID in the food industry. The technology has already been deployed at various upstream factories, logistics centers, and restaurants, with full-scale testing completed in several McDonald's outlets. The next phase includes nationwide implementation, with more than 100 supplier factories expected to be integrated into this system.
According to McDonald's China's Vice President of Supply Chain, Shi Yun, the technology's impact has been dramatic, with operational efficiency increasing by over 40% after the digital upgrade. Despite facing challenges in applying RFID to liquid products and metal packaging, McDonald's successfully overcame these obstacles, further pushing the boundaries of how RFID can be utilized in the food industry.
Key Benefits of the "One Box, One Code" System
1. Enhanced Traceability for Food Safety
The food and beverage supply chain is notoriously complex, making it challenging to accurately track products from production to retail. Lack of traceability can delay or complicate product recalls, thereby putting consumer safety at risk. With the "One Box, One Code" system, McDonald's China assigns a unique digital identifier to each box, enabling seamless, real-time tracking throughout its supply chain. This helps McDonald's rapidly identify and recall any defective or compromised products, thereby enhancing food safety and increasing public trust.
2. Improved Supply Chain Efficiency
Traditional supply chain operations in the food industry often suffer from inefficiencies due to manual processes, logistical delays, and human errors. McDonald's China's implementation of the "One Box, One Code" system digitalizes inventory and logistics, reducing dependency on manual tracking. Automated tracking, real-time data visibility, and streamlined logistics significantly boost efficiency, improving the overall responsiveness for distribution and stock replenishment. McDonald's reports that these system upgrades have driven efficiency gains of over 40%, marking a major step forward in modernizing supply chain operations.
3. Strengthened Food Quality Control
Ensuring the safety and quality of food is a critical aspect of McDonald's supply chain strategy, especially given the risks of contamination or mishandling. The new digital tracking system provides granular visibility into product conditions, including monitoring environmental parameters like temperature during storage and transportation. This level of monitoring ensures that all safety protocols are adhered to, allowing McDonald's to detect and mitigate issues before products reach consumers, ultimately safeguarding public health and maintaining brand integrity.
4. Seamless Integration with Diverse Suppliers
Coordinating operations across a vast network of suppliers can often lead to inefficiencies and inconsistencies. With plans to integrate over 100 supplier factories into the "One Box, One Code" system, McDonald's will be able to maintain standardized data and communication across its supply chain. This level of integration ensures that every stakeholder—from producers to logistics partners—works within a unified framework, minimizing friction, reducing inefficiencies, and streamlining overall operations.
A Step Towards Building a Smarter Supply Chain
The "One Box, One Code" technology not only provides immediate operational benefits but also aligns with McDonald's larger vision of building an intelligent, visible, and adaptive supply chain system. By leveraging technology to transform how goods are managed, McDonald's China is setting a new benchmark for food safety, traceability, and efficiency within the industry. The strategic deployment of this solution positions McDonald's as a trailblazer in technological innovation within the foodservice sector, driving advancements that improve not just its own operations but also set new standards for others to follow.
Other Supply Chain Innovations to Watch
McDonald's China is not alone in its pursuit of supply chain innovation. Several companies worldwide have made significant strides in transforming supply chains through advanced technology:
-
Amazon's Warehouse Robotics: Amazon has employed a variety of advanced robots, including robotic arms (Robin and Cardinal) and autonomous mobile robots like Proteus, to increase efficiency and reduce injuries in its warehouses. These innovations help to speed up the order fulfillment process and enhance workplace safety.
-
Coles' AI-Powered Fulfillment Center: The Australian supermarket chain Coles opened a customer fulfillment center equipped with AI and robotics to process over 10,000 orders per day. This system optimizes stock availability, minimizes substitutions, and streamlines the online shopping process for customers.
-
Shein's On-Demand Supply Chain: Fast-fashion retailer Shein has developed an on-demand supply chain model that reduces inventory waste and shortens response times for new fashion trends. Shein now plans to offer this technology to other brands, potentially reshaping the dynamics of the fashion supply chain.
Conclusion
McDonald's China's adoption of the "One Box, One Code" technology exemplifies how leveraging cutting-edge technologies can address critical challenges in the supply chain. By providing real-time visibility, improving operational efficiency, and enhancing safety protocols, this digital transformation is setting McDonald's apart as a leader in the industry. As the system rolls out nationwide, it is poised to not only elevate McDonald's supply chain capabilities but also establish a new industry standard, encouraging others to embrace similar innovations for the betterment of food safety, quality control, and operational excellence.